O Instituto de Energia Solar Francesa Ines desenvolveu novos módulos fotovoltaicos com termoplásticos e fibras naturais fornecidas na Europa, como linho e basalto. Os cientistas pretendem reduzir a pegada ambiental e o peso dos painéis solares, enquanto melhoram a reciclagem.
Um painel de vidro reciclado na frente e um composto de linho na parte traseira
Imagem: GD
Da revista PV França
Pesquisadores do Instituto Nacional de Energia Solar da França (INES)-uma divisão das energias alternativas francesas e Comissão de Energia Atômica (CEA)-estão desenvolvendo módulos solares com novos materiais biológicos nas laterais dianteiras e traseiras.
"À medida que a pegada de carbono e a análise do ciclo de vida se tornaram critérios essenciais na escolha de painéis fotovoltaicos, o fornecimento de materiais se tornará um elemento crucial na Europa nos próximos anos", disse Anis Fouini, diretor da CEA-ENSES , em uma entrevista à revista PV France.
Aude Derrier, coordenadora do projeto de pesquisa, disse que seus colegas analisaram os vários materiais que já existem, para encontrar um que possa permitir que os fabricantes de módulos produza painéis que melhorem o desempenho, a durabilidade e o custo, enquanto diminuem o impacto ambiental. O primeiro demonstrador consiste em células solares de heterojunção (HTJ) integradas a um material todo composto.
"A parte da frente é feita de um polímero cheio de fibra de vidro, que fornece transparência", disse Derrier. "O lado traseiro é feito de composto com base em termoplásticos nos quais uma tecelagem de duas fibras, linho e basalto, foi integrada, o que fornecerá força mecânica, mas também melhor resistência à umidade".
O linho é proveniente do norte da França, onde todo o ecossistema industrial já está presente. O basalto é adquirido em outros lugares da Europa e é tecido por um parceiro industrial da Ines. Isso reduziu a pegada de carbono em 75 gramas de CO2 por watt, em comparação com um módulo de referência da mesma potência. O peso também foi otimizado e é inferior a 5 kg por metro quadrado.
"Este módulo é voltado para o PV da cobertura e a integração de edifícios", disse Derrier. “A vantagem é que ela é naturalmente de cor negra, sem a necessidade de uma fábrica. Em termos de reciclagem, graças aos termoplásticos, que podem ser restringidos, a separação das camadas também é tecnicamente mais simples. ”
O módulo pode ser feito sem adaptar os processos atuais. Derrier disse que a idéia é transferir a tecnologia para os fabricantes, sem investimentos adicionais.
"O único imperativo é ter freezers para armazenar o material e não iniciar o processo de reticulação de resina, mas a maioria dos fabricantes hoje usa pré-registro e já está equipada para isso", disse ela.
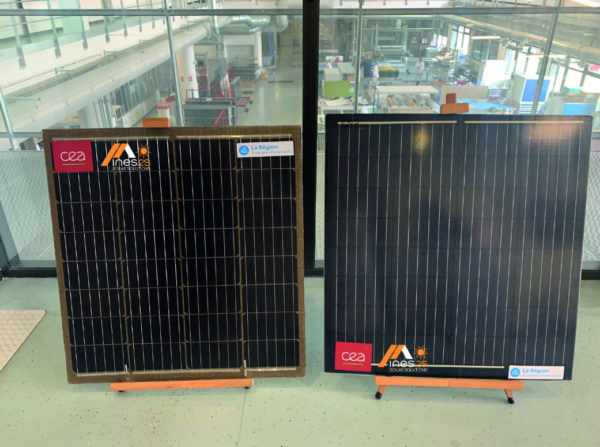
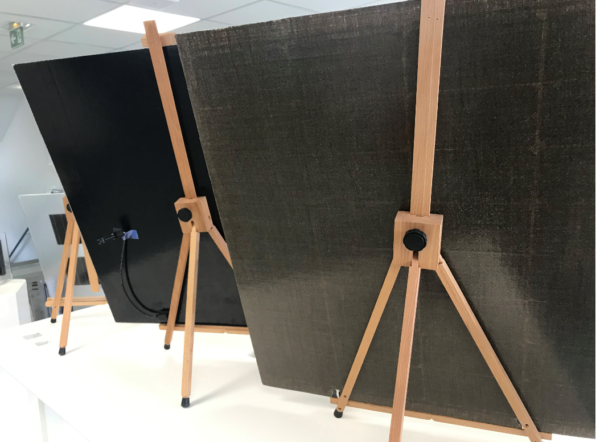
"Trabalhamos no Second Life of Glass e desenvolvemos um módulo composto de vidro reutilizado de 2,8 mm que vem de um módulo antigo", disse Derrier. "Também usamos um encapsulante termoplástico que não requer reticulação, que, portanto, será fácil de reciclar e um composto termoplástico com fibra de linho para resistência".
A face traseira sem basalto do módulo possui uma cor de linho natural, que pode ser esteticamente interessante para os arquitetos em termos de integração da fachada, por exemplo. Além disso, a ferramenta de cálculo da INES mostrou uma redução de 10% na pegada de carbono.
"Agora é imperativo questionar as cadeias de suprimentos fotovoltaicos", disse Jouini. “Com a ajuda da região do Rhône-Alpes, dentro da estrutura do Plano de Desenvolvimento Internacional, procuramos jogadores fora do setor solar para encontrar novos termoplásticos e novas fibras. Também pensamos no atual processo de laminação, que é muito intensivo em energia. ”
Entre a pressurização, a prensagem e a fase de resfriamento, a laminação geralmente dura entre 30 e 35 minutos, com uma temperatura operacional de cerca de 150 ° C a 160 C.
"Mas para módulos que incorporam cada vez mais materiais ecológicos, é necessário transformar termoplásticos em cerca de 200 ° C a 250 ° C, sabendo que a tecnologia HTJ é sensível ao calor e não deve exceder 200 ° C", disse Derrier.
O Instituto de Pesquisa está se unindo ao especialista em termocompressão de indução baseado na França, Roctool, para reduzir os tempos de ciclo e fazer formas de acordo com as necessidades dos clientes. Juntos, eles desenvolveram um módulo com uma face traseira feita de compósito termoplástico do tipo polipropileno, ao qual foram integradas fibras de carbono recicladas. A parte frontal é feita de termoplásticos e fibra de vidro.
"O processo de termocompressão de indução de Roctool permite aquecer rapidamente as duas placas dianteiras e traseiras, sem ter que atingir 200 ° C no núcleo das células HTJ", disse Derrier.
A empresa afirma que o investimento é menor e o processo pode atingir um tempo de ciclo de apenas alguns minutos, enquanto usa menos energia. A tecnologia visa os fabricantes compostos, para dar a eles a possibilidade de produzir partes de diferentes formas e tamanhos, enquanto integra materiais mais leves e duráveis.
Horário de postagem: junho-24-2022